Bionic Men
ENG alums help advance lifelike prosthetic leg

The iWalk BiOM prosthetic ankle enables amputees to walk naturally and effortlessly. Photos courtesy of iWalk
A breakthrough robotics technology is enabling a growing number of amputees to walk naturally and effortlessly.
In recent years, carbon fiber technology has made possible the production of lighter, stronger artificial limbs that provide increased mobility to injured soldiers, people with diabetes, and others with missing or impaired lower limbs. But moving about with a carbon fiber prosthetic can be like walking in sand: putting one foot in front of the other takes up to 50 percent more energy than that expended by people with natural limbs.
That’s where a new prosthetic ankle, the BiOM by iWalk, Inc., commercially available since September 2011, comes in. Supplying that extra energy through batteries, motors, and springs, the 4.5-pound BiOM replicates the action of the foot, Achilles tendon, and calf muscles to provide powered plantar flexion, or push-off.
Among the 60 iWalk employees who are shaping the future of bionic technology at the Bedford, Mass.–based start-up are three College of Engineering mechanical engineering alumni—Weston Smith (ENG’11), Josh Prescott (ENG’11), and Chris Park (ENG’11). They are part of iWalk’s effort to rebuild and restore natural motion from the ground up to potentially millions of affected individuals.
Witnessing the transfer of iWalk’s technology to veterans and active-duty soldiers has been the greatest on-the-job reward, says Smith, who started working for the company as a quality engineer in October 2010.
“It was neat to send our first commercial shipment of prosthetic ankles to Walter Reed National Military Medical Center and be there to see people walk on them for the first time,” he says.
Now working as a manufacturing engineer, Smith’s job is to improve the manufacturing process and incorporate design improvements into iWalk’s production line. It’s the job he set his sights on in 2009, when he was a lab technician without engineering credentials at a medical device company. With an undergraduate degree in visual arts and experience as a cabinetmaker and carpenter, he enrolled in ENG’s Late Entry Accelerated Program (LEAP), which permits nontraditional students and working professionals to obtain a graduate degree in engineering, as the ticket to his dream job.
“I couldn’t find anything else like it in the country,” Smith recalls. “Having the chance to study engineering after having been on a different path helped me to be really flexible, which is what’s required here. It’s a small enough place that we all do a little bit of everything beyond our core engineering tasks, from writing marketing materials to delivering the product to customers.”
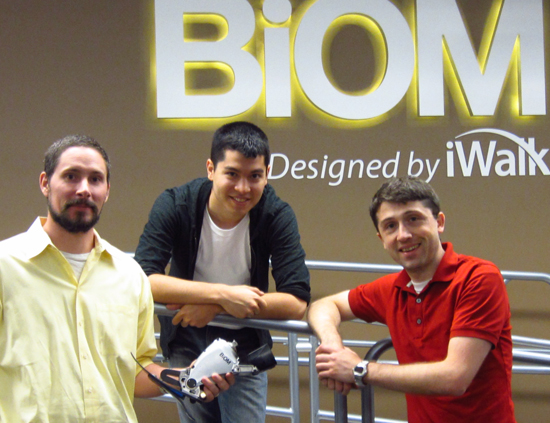
Noting iWalk’s appreciation for versatile, team-oriented employees, traits encouraged by the setup of the company’s main office—low-rise cubicles allowing employees to see what everyone else is doing—Smith urged Prescott, a fellow LEAP student, to interview at the company in March 2011. The quality manager hired him on the spot.
Currently a research and development engineer, Prescott is working on advancing a number of new iWalk product concepts that could extend the BiOM platform to support other parts of the lower leg. Like Smith, however, he didn’t always have the technical skills needed for this work.
As an undergraduate at Hampshire College, he created his own major in assistive design, working on new concepts for wheelchairs and other medical devices. While designing products for a few small businesses, he realized that he needed to expand his skill set so he could carry an invention from concept to product, and so he enrolled in the LEAP program, where he focused on product design and analysis.
“I always had good engineering instincts, but BU gave me the technical skills that I needed to truly design,” Prescott says. “Here, I’ve been able to apply those skills to solve complex real-world problems, such as analyzing data that we get from the prosthetic ankle to quantify how well the product is replicating the functionality of a biological ankle.”
Chris Park, who has worked at iWalk as a mechanical engineer since August 2011, also learned about the company from Smith, who had recommended him for a research assistant position while at BU.
“Weston used to joke that he was becoming my personal HR department,” says Park.
Today he spends much of his time upgrading designs for BiOM components, with the goal of making the device more affordable without compromising effectiveness or durability. Part of this effort involves design for manufacturing—engineering parts so they are easier to machine, thus saving time and money—a capability that Park first honed during long hours in ENG’s machine shop.
“Working for iWalk has been an incredible educational experience,” Park says. “Everyone I’ve met here is really exceptional.”
Perhaps that’s because what drives Smith, Prescott, Park, and their coworkers is the opportunity to realize an exceptional vision, championed by iWalk’s founder, Hugh Herr: to create the world’s first prosthetic devices that feel and act like biological limbs, thereby vastly improving users’ mobility and overall quality of life.
“I knew that if the job was for a cause I could feel good about, that’s the kind of place I wanted to work for,” says Park.
Mark Dwortzan can be reached at dwortzan@bu.edu.
A version of this article originally ran in the fall 2012 ENGineer magazine.
Comments & Discussion
Boston University moderates comments to facilitate an informed, substantive, civil conversation. Abusive, profane, self-promotional, misleading, incoherent or off-topic comments will be rejected. Moderators are staffed during regular business hours (EST) and can only accept comments written in English. Statistics or facts must include a citation or a link to the citation.