Where You Bring Ideas Into Reality
New EPIC Director Anna Thornton sees the cutting-edge facility as a place where faculty, students and industry work together to solve engineering challenges
With a broad vision for the high-tech manufacturing and design space at the heart of Boston University’s campus, Professor of the Practice Anna Thornton (ME) has taken the reins as the new director of the Engineering Product Innovation Center (EPIC). High on her “10-page to-do list,” she says on a recent visit to the space, is a plan to spread the word that EPIC isn’t just a machine shop but a center where faculty, staff, and industry work together to teach students how to bring their ideas and theory into reality.
The center’s 15,000 square feet of space is filled with cutting-edge manufacturing equipment, from CNC mills and lathes to the latest model 3D printers and everything in between. “These are precise, expensive, very capable tools,” says Thornton. “These are the kinds of manufacturing methods that ENG students are going to see and use in industry.” In addition, the space is staffed by five, highly trained lab supervisors who have incredible experience in machining, design, electronics, and education.
Students from across ENG departments learn how to use these machines to build prototypes. But EPIC isn’t just a machine shop, says Thornton. “It’s a resource for solving problems.” Designs and ideas rarely work on the first try. Students learn how to debug their designs, work with experts to review their concepts and continue to refine and improve their ideas.
More than that, EPIC is a bridge between engineering theory and practice. “In order to create a product, you have to actually physically substantiate your theory,” Thornton says. “And this is where that happens.”
Thornton knows all about that intersection between plans and production. Over two decades as a consultant and practicing engineer, she has helped scores of companies launch products, in industries ranging from aerospace and railroads to sports equipment and medical devices. She joined BU in 2017 and has taught courses such as ME537 Product Realization (also the title of her new book) and the undergraduate ME358 Manufacturing Processes.
The new EPIC director came by her interest naturally. Her father was a chemical engineer, and her grandfather ran manufacturing for International Harvester. As a teenager, she got to tinker with tractors and use the equipment in her father’s workshop. To this day, Thornton builds furniture in her spare time. As a mother, she helped her then-11-year-old daughter figure out how to 3D print a model of a virus.
“But not everybody had that exposure” to the tools and principles of manufacturing, Thornton points out. “Though I feel very comfortable walking the factory floor, I get that it can be intimidating to walk into a big, noisy room full of big equipment” Indeed, most incoming ENG students don’t have hands-on manufacturing experience, she says, and neither do many of the Sargent College or College of Fine Arts students who use the space for everything from building new assistive devices to fabricating art installations.
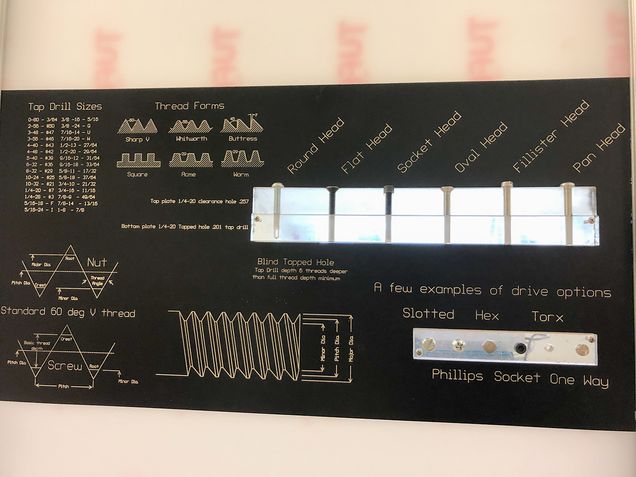
That’s why Thornton is launching a series of initiatives aimed at educating the BU student body about what EPIC has to offer, and making it easier for aspiring product developers to get started. For example, the EPIC website hosts how-to videos for all the equipment. Inside the shop, moveable “means boards” provide diagrams, specs, and physical samples showing, for example, how to mount bearings. The center is hosting a range of tours and short courses on everything from sketching to 3D printing to machining. In addition, EPIC is sponsoring a number of talks from industry sponsors and finding relevant and exciting senior capstone projects for students to work on. “Creating opportunities for students to interact with industry really energizes the students. They better understand how the curriculum will help them be a better engineer in the future. Our industry partners love to hire students with experience in EPIC.”
In addition to supporting the many hands-on classes across the University, EPIC is also striving to proactively fill in common gaps in students’ knowledge. Rather than a place for hardened gearheads, EPIC is a place for students to learn how to refine their plans and drawings, think through ways to build, select the right materials, and safely use a cold saw, drill press, or CNC lathe, all under the guidance ofexpert staff.
Thornton points out that students often don’t internalize what they learn in the classroom until they get their hands on a machine and start making stuff. “We learn in class how to compute the power required to remove material at a certain rate,” says Thornton. “Then here in EPIC, they can see the chips flying off the part and ask, ‘What is that awful sound when I cut too fast?’ and they can feel how warm the part gets. It becomes a learning moment. Trouble-shooting, challenging the assumptions, going back and doing more calculations—that’s how students integrate the experiences and really learn the material.”
On a return visit to EPIC a week later, Thornton says that her to-do list has doubled, to 20 pages.
“It’s going to be a lot of work,” she says. “But it’s a real privilege, and I’m excited and grateful to have the opportunity to help students get excited about seeing how the theory they learn in the classroom translates into something they can build.”