It’s Now Possible to Print a Face in 4D

It’s Now Possible to Print a Face in 4D
BU engineer unveils a method for printing structures that first appear flat, but then transform into extremely complex shapes, like a human face
What would it take to transform a flat sheet of material into a mask-like relief of a human face, triggered simply by a change in environment? How would the sheet warp itself into the concave shapes of the eye sockets and the convex protrusions of the nose and chin?
Over the past decade, scientists have found inspiration in nature—like the way that plants and flowers unfurl their leaves and blooms—as they have sought to develop new materials and techniques for 3D and 4D printing, where the fourth dimension represents a structure’s ability to transform its shape over time, much like a flower blossoming. But complex curvature—the kind of shape-shifting that it would take to turn a flat sheet of material into something resembling a human face—has remained out of reach. Until now.
A new 4D-printing technique uses latticework composed of multiple materials that grow or shrink in response to environmental changes, finally making the most complex shape changes possible. The research team, including William Boley, a Boston University College of Engineering assistant professor of mechanical engineering, has published their results in Proceedings of the National Academy of Sciences.
“By printing materials with different thermal expansion behavior in predefined configurations, we can control the growth and shrinkage of each individual ‘rib’ of the lattice, which in turn gives rise to complex bending of the printed lattice,” says study co–lead author Boley, who began work on the project as a postdoctoral research fellow at Harvard University’s John A. Paulson School of Engineering and Applied Sciences (SEAS).
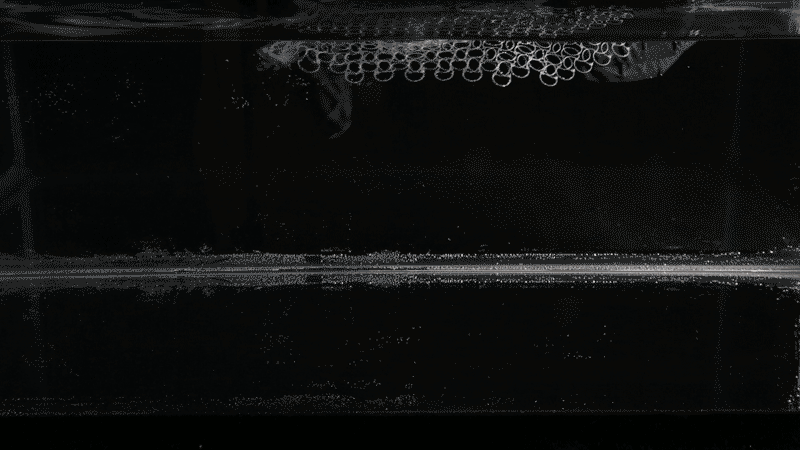
To showcase the abilities of the method, the team chose to mimic the face of the 19th-century mathematician who first laid the foundations of differential geometry: Carl Friedrich Gauss. The researchers analyzed a 2D portrait of Gauss, painted by Christian Albrecht Jensen in 1840, using a machine-learning algorithm that helped them adapt that 2D image into a digital 3D profile of Gauss’ features. Then, using the 3D profile as a guide, they printed in 3D a flat latticework of different material layers, designed to grow, flex, and shrink in response to environmental changes in precise ways that would recreate the unique curves of Gauss’ face. Upon dropping the flat latticework into a tank of saltwater, it responds to the change in salinity and morphs into Gauss’ likeness.
“The open cells of the curved lattice give it the ability to grow or shrink a lot, even if the material itself undergoes limited extension,” says study co–lead author Wim M. van Rees, who like Boley is also a former postdoctoral fellow at Harvard, and is now an assistant professor at MIT.
But to achieve complex curves, growing and shrinking the lattice on its own isn’t enough. You need to be able to direct the growth locally.
“That’s where the materials palette that we’ve developed comes in,” says Boley. The team employed four different materials and programmed each “rib” of the lattice to change shape in special ways.
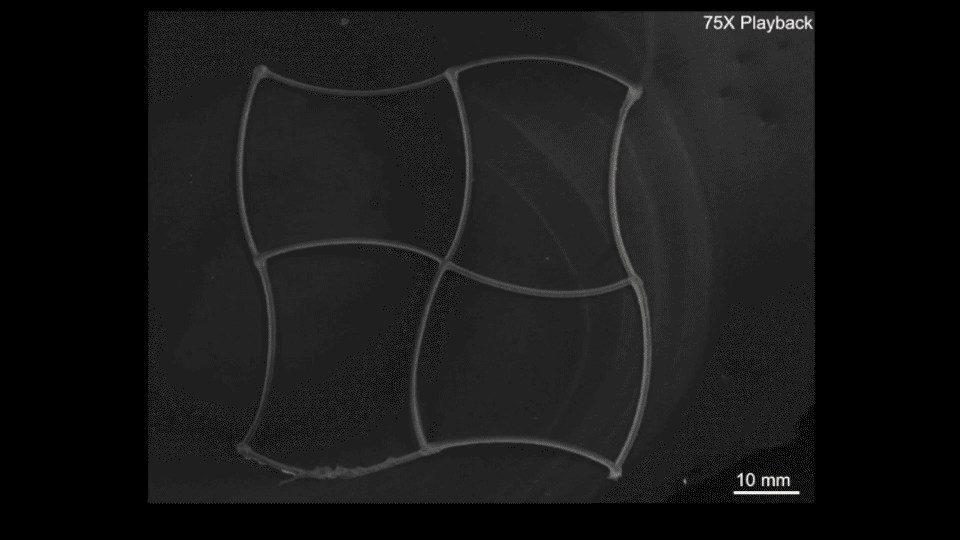
As a second demonstration, they also printed a more practical product of their method: a shape-shifting, low-profile radio antenna (called a “patch” antenna), which can adopt different frequencies as it changes shape.
“Together, we are creating new classes of shape-shifting matter,” says Jennifer A. Lewis, a Harvard professor of biologically inspired engineering and study co–corresponding author. “Using an integrated design and fabrication approach, we can encode complex ‘instruction sets’ within these printed materials that drive their shape-morphing behavior.” Lewis is also a core faculty member of the Wyss Institute for Biologically Inspired Engineering at Harvard University.
This design approach and multimaterial 4D-printing method could be extended to other stimuli-responsive materials and be used to create scalable, reversible, shape-shifting structures with unprecedented complexity. Based on their experimental successes, the team envisions that the 4D-printing technique could have uses in many different industrial and research areas. “Application areas include soft electronics, smart fabrics, tissue engineering, robotics, and beyond,” says Boley.
This research was supported by the National Science Foundation and Draper Laboratory.
This story was adapted from a Harvard news release written by Leah Burrows.
Comments & Discussion
Boston University moderates comments to facilitate an informed, substantive, civil conversation. Abusive, profane, self-promotional, misleading, incoherent or off-topic comments will be rejected. Moderators are staffed during regular business hours (EST) and can only accept comments written in English. Statistics or facts must include a citation or a link to the citation.